MIG welding with cast iron presents both challenges and opportunities that can greatly influence any welding project involving this notoriously tough material. While cast iron's strength is undeniable, its composition poses unique challenges to even the most seasoned welders.
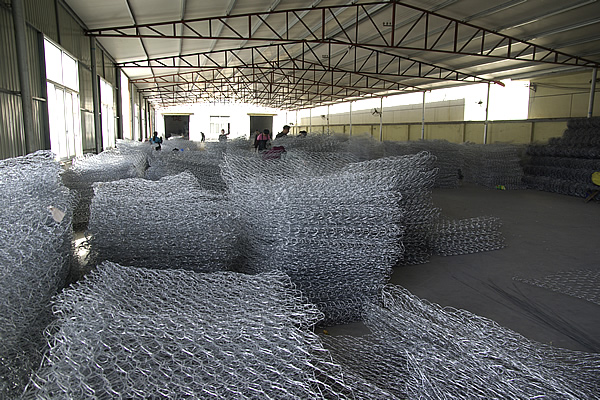
The first step in mastering MIG welding with cast iron is understanding the material itself. Cast iron typically contains 2-4% carbon and varying degrees of silicon, affecting its thermal expansion and contraction—a key factor when welding. Oddly enough, this high carbon content, responsible for cast iron’s renowned strength, is also its Achilles’ heel during welding. The risk of cracking is substantial, predominantly due to uneven heating and cooling cycles.
To counter these issues, preheating is crucial. Heating the cast iron piece to a temperature between 500°F and 1200°F helps to minimize thermal shock. The preheat temperature is determined by the thickness and complexity of the component. Additionally, maintaining the heat throughout the welding process and allowing the piece to cool slowly post-welding is essential to mitigate the cracking risks.
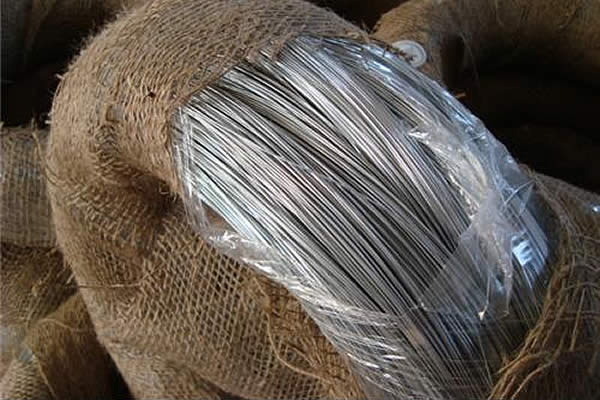
Selecting the right filler material is another critical choice in MIG welding cast iron. Typically, a nickel-based filler rod or wire is used due to its similarity in thermal expansion properties with cast iron. Nickel's ductility allows it to absorb some of the stress from the weld area, reducing the risks of cracking. In some cases, a pure nickel rod is preferred for its machinability and softness, which make the post-weld process smoother.
mig cast iron
However, MIG welding’s inherent limitation is its heat control, which is why technique is paramount. Short arc welding is often recommended to keep the heat input low and easily manageable. This approach involves using a lower voltage and wire feed speed, reducing the chances of thermal distortion and associated cracking. Additionally, executing a series of tack welds to temporarily secure the materials, before proceeding with a full weld, helps maintain structural integrity.
While MIG welding cast iron is within reach, the process demands thorough preparation and a deep comprehension of both materials and methodology. Having extensive expertise and authority in this field not only improves weld quality but ensures a level of trustworthiness that is vital for long-term success. Additionally, leveraging experience from practice and trial-and-error can greatly expedite the learning curve.
A professional with significant experience in MIG welding cast iron is invaluable, as their insight can prevent errors that a novice might overlook. Conversely, beginners should not shy away but rather seek mentorship from veteran welders or engage with specialized resources like industry workshops or online communities. Adopting a detail-oriented approach coupled with a thirst for continuous improvement ensures not only the integrity of the final weld but also growth as a skilled welder recognized for expertise, authority, and trustworthiness.
In conclusion, MIG welding with cast iron demands respect for the material, appropriate techniques, and suitable tools. Successfully navigating this challenging yet rewarding practice can elevate one's craftsmanship to heights others might merely aspire to. The journey from competence to mastery is paved with persistence, precision, and patience—key cornerstones in the art of welding.