Welding cast iron with stainless steel wire presents a unique challenge due to the significant differences in their material properties. However, when executed correctly, this process can result in durable, high-quality joints that leverage the strengths of both materials. Drawing from years of hands-on experience and expert insights, this article explores the intricacies of joining these metals, ensuring reliable outcomes and maintaining structural integrity.
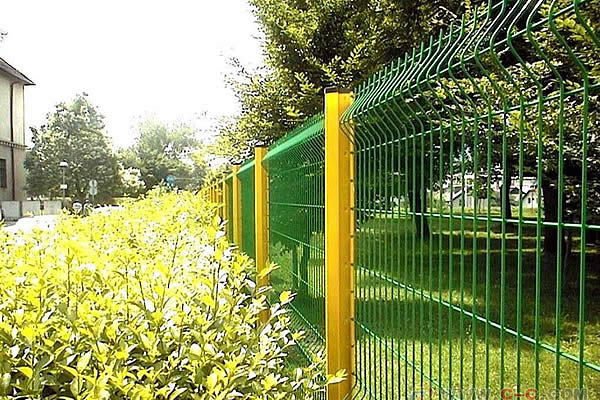
Cast iron, a carbon-rich alloy, is known for its brittleness and susceptibility to cracking when subjected to thermal stresses. Stainless steel, on the other hand, boasts strength, corrosion resistance, and ductility. Combining these materials requires careful consideration of their thermal expansion rates, melting points, and mechanical properties.
Preparation is critical before initiating the welding process. Clean the surfaces meticulously to remove contaminants like grease, oil, and rust, which can exacerbate porosity and lead to weak welds. Preheating the cast iron is often recommended to about 250-500°F (120-260°C) to minimize thermal shock and reduce the risk of cracking from rapid temperature changes. This step is vital as it helps to equalize the temperature between the welding arc and the surrounding area, easing the stress on the cast iron.
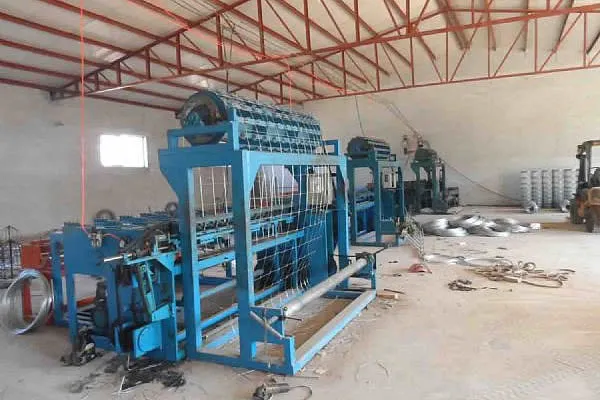
Selecting the right stainless steel wire is another pivotal factor.
A popular choice is the 309L or 312 stainless steel wire. These filler materials offer a high level of corrosion resistance and excellent crack resistance, which suits the brittle nature of cast iron. The chromium content in these alloys forms a strong bond while providing the necessary flexibility to accommodate any thermal contractions or expansions.
Using appropriate welding techniques further enhances success. Many professionals favor the shielded metal arc welding (SMAW) or the gas metal arc welding (GMAW) processes. When employing SMAW, choose a low amperage setting; keeping the heat input low is essential to prevent undue stress on the cast iron. Short, narrow beads help control the weld temperature. It's wise to use a peening technique after each weld; this involves gently hammering the weldment to release residual stresses and counteract distortion tendencies.
welding cast iron with stainless steel wire
During the welding operation, maintain an interpass temperature to bolster the structural integrity of the welds. Keeping track of temperature changes using digital pyrometers can provide real-time data, ensuring that the entire piece stays within the optimal temperature range.
Post-weld, allow the material to cool gradually. Rapid cooling can induce thermal shock, leading to cracks. Some professionals advocate for wrapping the piece in insulation blankets to ensure even cooling, which can be crucial in maintaining the weld's strength and durability.
Expertise in welding these materials isn't just about technical know-how; it also involves understanding the real-world applications. For instance, the automotive and construction industries often necessitate this welding method due to specific mechanical demands. In these sectors, ensuring the longevity and resilience of the welded joint is paramount. Experienced welders constantly update their skills and stay abreast of the latest technology and methodologies, which are often found in technical white papers and industry seminars.
Authoritative insight comes from continuous learning and adaptation. Professionals understand that no two welding projects are identical. Variables such as the grade of the cast iron, the stainless steel composition, and environmental factors can all influence the welding process. Respect for the nuanced nature of these projects underlines the trustworthiness of an experienced welder.
In summary, welding cast iron with stainless steel wire isn't merely a task; it's a sophisticated craft requiring careful attention to detail, comprehensive material understanding, and proficient execution. When done correctly, these welds not only achieve desired functionality but also demonstrate exemplary craftsmanship. As industries advance, the synergy of these metals will continue to unveil innovative uses and robust applications, securing their place in both traditional and modern manufacturing landscapes.