When choosing the correct materials in welding, 304 welding wire often emerges as a preferred choice among industry professionals. The 304-grade stainless steel is not just any material; it holds a distinctive position due to its composition, properties, and performance in diverse welding applications.
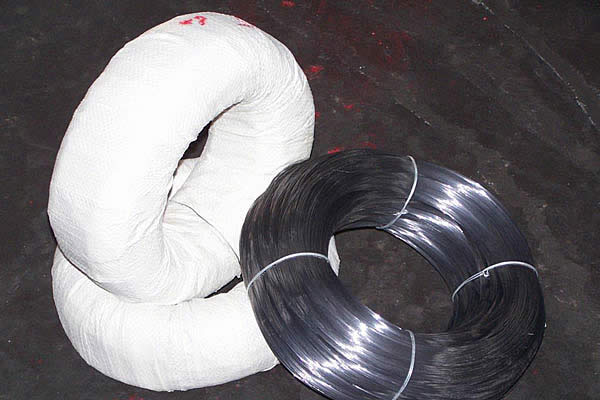
304 stainless steel, known for its corrosion resistance, forms the backbone of 304 welding wire. This specific grade includes 18% chromium and 8% nickel, a composition that offers the advantage of robust resistance against intergranular corrosion, making it excellent for welding applications exposed to environmental factors that accelerate wear and tear.
From an experience standpoint, welders find 304 welding wire versatile. Whether executing a MIG (Metal Inert Gas) or TIG (Tungsten Inert Gas) welding process, users appreciate the ease with which it melts and flows, ensuring strong welds and clean lines. This wire's low carbon content further minimizes carbide precipitation. This characteristic reduces the risk of corrosion, a fact seasoned welders leverage to maintain the longevity and durability of their welds.

Moreover, professionals in the industry trust 304 welding wire because of its outstanding versatility across different applications. It is not limited to a specific sector but finds utility in various industries including food processing, pharmaceuticals, and even aerospace engineering. Its non-reactivity and sanitary properties adhere to the rigorous standards of clean industrial applications, ensuring safety while maintaining high quality.
In terms of expertise,
understanding the nuances of welding with 304 wire involves recognizing its operating limitations. While its stainless steel nature provides ample advantages, the welder's skill lies in managing heat input correctly during the welding process. Excessive heat can lead to distortion or compromise the integrity of the weld joint. Professional welders control these parameters to produce optimal results, leveraging shielding gases like argon or helium to fine-tune the welding environment, ensuring the weld pool is protected from atmospheric contaminants.
304 welding wire
Authoritativeness in using 304 welding wire also comes from certifications and manufacturing standards met by quality suppliers. Wire manufacturers often subject their products to ASTM standards, guaranteeing the wire's performance meets stipulated industry criteria. Professionals should check for these certifications, adding a layer of trust and ensuring that the material quality lives up to client expectations and project specifications.
Choosing 304 welding wire instills trust for project managers focused on sustainability. Its corrosion-resistant properties ensure that structures maintain their integrity over time, circumventing costly repairs or replacements. This material's resilience equates to fewer maintenance interventions, aligning with cost-saving strategies and sustainable practices focused on the lifecycle of welded products.
Furthermore, when considering indoor or outdoor applications, where exposure to moisture, extreme temperatures, or chemicals is a possibility, the inherent properties of 304 welding wire provide a reliable safeguard. The chromium layer, vital for stainless steel’s resistance to oxidation, becomes a pivotal element that prevents surface degradation, securing structures against the unpredictabilities of both artificial and natural environments.
The thoughtful application of 304 welding wire goes beyond mere product choice; it manifests as a strategic decision backed by professional expertise and an understanding of its multifaceted benefits. By combining appropriate techniques and leveraging its intrinsic properties, professionals ensure strong, reliable, and enduring welds. This approach does not only ensure professionalism but elevates operational trust and builds on the authority of using tried-and-tested materials within the welding community.
Combatting corrosion, ensuring environmental adaptability, and contributing to structural sustainability, the 304 welding wire remains unmatched. It stands not merely as a material option but embodies a holistic solution that transcends ordinary application, achieving reliable, authoritative, and trusted results time and again.