Flux core welding cast iron can be a challenging task, yet with the right approach and materials, it's entirely possible to achieve strong, lasting welds. Cast iron, known for its brittleness and diverse composition, requires specific techniques to ensure structural integrity. An experienced welder understands the nuances of using flux core welding, particularly with cast iron, offering an effective solution for repairs and fabrications.

Flux core welding (FCAW) is advantageous for its versatility and efficiency, especially in outdoor or challenging environments. This method, utilizing a flux-filled tubular wire, reduces the need for a separate shielding gas, making it particularly suitable for windy conditions. When applied to cast iron, the choice of wire, preheating, and cooling procedures are crucial.
Choosing the appropriate wire is a foundational element. Nickel-based wires are generally preferred for welding cast iron due to their compatibility in reducing the risk of cracking. These wires can absorb the thermal expansion differences between cast iron and the weld material, mitigating the brittleness commonly associated with cast iron welding. Additionally, nickel wires prevent the carbon migration from the cast iron base material, maintaining the weld's integrity.
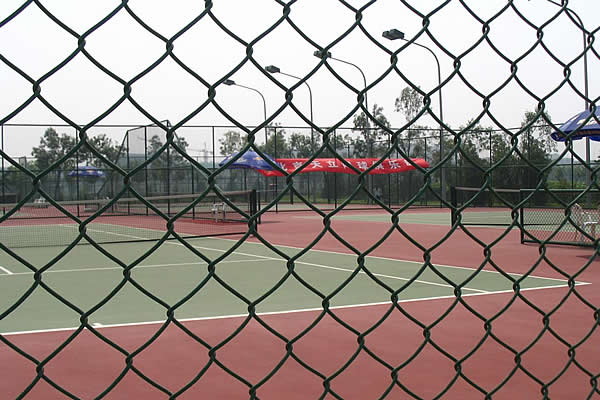
Preheating the cast iron is another critical step. Cast iron's thermal expansion properties mean that significant temperature fluctuations can cause cracking. By gradually and uniformly preheating the material to temperatures between 500°F and 1200°F (260°C to 650°C), the welder can reduce thermal shock and enhance the ductility of the piece. Uniform heating ensures that residual stresses are minimized, which is crucial given cast iron's inherent brittleness.
Once welding begins, managing the cooling process is equally important. Slow cooling rates are recommended to prevent the formation of hard, brittle phases in the material. Wrapping the welded piece in insulation blankets after welding can aid in achieving this controlled cooling rate, helping to maintain the weld's ductility and reduce the risk of cracking.
In terms of technique, short, thin weld passes are recommended to limit the heat input and minimize stress concentrations in the heat-affected zone. Applying a back-and-forth motion can help deposit the material evenly and enhance the bond. It's also advisable to peen the weld between passes. Peening helps relieve tensile stresses within the weld bead as it cools, an essential step in maintaining the weld's structural integrity.
flux core welding cast iron
Ensuring a clean workpiece is another crucial aspect of welding cast iron. Contaminants such as oil, grease, or rust can significantly affect the quality of the weld. Proper cleaning with solvents and mechanical methods (such as grinding) ensures a sound, defect-free bond. This preparation is vital given the porous nature of cast iron, which can trap impurities and lead to weak joints.
Post-weld treatment including stress-relief techniques is also recommended. Heat treating the completed weld further alleviates internal stresses and stabilizes the material. This final step can be the difference between a durable weld and one prone to failure over time.
Experience with flux core welding of cast iron highlights the need for meticulous planning and execution. Each stage, from material preparation, preheating, and welding to post-weld cooling and treatment, needs careful attention to detail. The welder’s expertise ensures a successful outcome, reflecting a deep understanding of both the material and the welding process.
In industry, this knowledge translates into reliable repairs of machinery, engine blocks, and structural components, where durability and strength are non-negotiable. While the challenges are non-negligible, the satisfaction of restoring and reinforcing cast iron components showcases the welder's skill and dedication to their craft.
With flux core welding, the adaptation to various working conditions without compromising the quality of the weld demonstrates the method's effectiveness. It emphasizes the importance of using the correct parameters and techniques for a successful cast iron welding project, underscoring the expertise and authority required in this specialized field.