Iron wire is an indispensable component in various industries, renowned for its myriad applications and versatility. Understanding the intricacies of its use can significantly benefit businesses and individuals alike, ensuring efficiency, durability, and innovation.
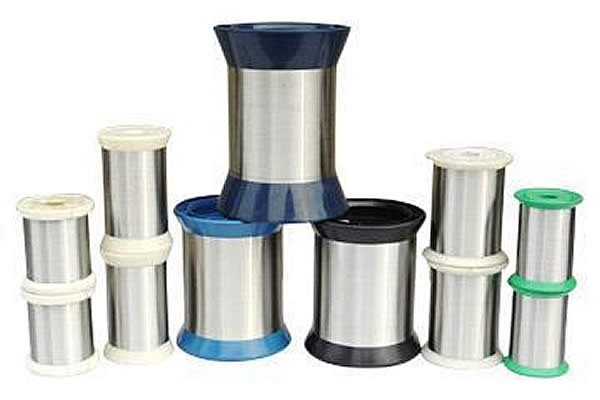
Iron wire comes in various types, including galvanized, annealed, and stainless wire, each serving distinct purposes. Galvanized iron wire is coated with zinc, making it resistant to corrosion, which is vital for outdoor and industrial applications where exposure to moisture and other elements is a concern. This type of wire is often utilized in fencing, fabrication of wire mesh, and even in the creation of craft items.
Annealed iron wire,
on the other hand, is known for its pliability. The annealing process involves heating the wire and then slowly cooling it, enhancing its elasticity and reducing brittleness. This flexibility makes annealed wire ideal for binding, tying, and crafting applications where malleability is crucial. It is a favorite in construction sites for tying rebar and in the agriculture industry for hay baling.
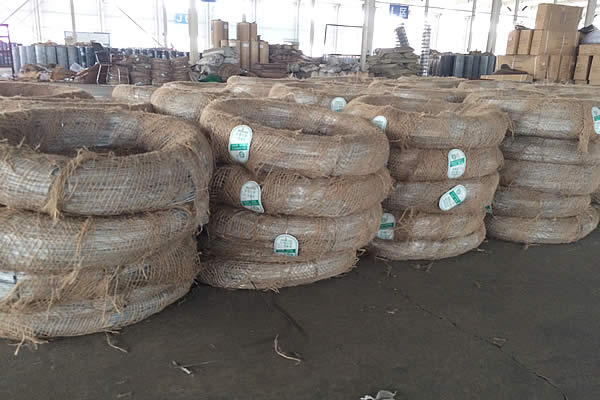
For projects demanding durability and resistance to harsh environments, stainless iron wire is the go-to choice. Its high resistance to rust and corrosion makes it perfect for high-moisture and coastal areas. Stainless wire is extensively used in the food industry, medical equipment manufacturing, and architectural designs that aim for longevity and aesthetic appeal.
Innovations in iron wire technology continue to shape industry standards, with manufacturers focusing on improving strength, flexibility, and coating quality. These advancements not only enhance the wire’s performance but also extend its application across emerging fields like renewable energy, where iron wire can be integral in solar panel mounting systems and wind turbine assemblies.
Selecting the appropriate wire type requires expertise and a deep understanding of project-specific needs. Factors such as environment, load requirements, and budget must be considered to ensure optimal selection. Consultation with professionals or manufacturers can provide critical insights, ensuring the chosen iron wire meets all necessary specifications and standards for safety and performance.
wire for iron
Authoritative resources stress the importance of sourcing iron wire from reputable suppliers to guarantee quality and compliance with international safety standards. Certifications and compliance documents should be requested and reviewed during the purchasing process to establish trustworthiness. This diligence helps in mitigating risks associated with substandard materials, which can lead to structural failures or increased maintenance costs.
Real-world experiences underline the significance of proper installation and maintenance of iron wire products. Regular inspections for signs of wear, rust, or tension loss can extend the lifespan of the wire, ensuring continued reliability and safety. In industries where iron wire is subjected to constant stress and environmental exposure, implementing a maintenance schedule can prevent costly downtimes and accidents.
Emphasizing eco-friendly practices, the recycling of iron wire is gaining attention as an effective way to manage resources efficiently. Scrap iron wire can be melted down and reused, reducing environmental impact and promoting sustainability within the industry. Companies implementing recycling strategies often find financial benefits through reduced waste disposal costs and the resale of recycled materials.
For those keen to dive deeper into the technical aspects of iron wire, trade publications and scholarly articles offer extensive research and case studies. These sources provide insider knowledge into the latest trends, technological advancements, and future prospects of iron wire production and application.
Conclusively, iron wire, with its various types and endless applications, remains a vital material across numerous sectors. It requires a balance of practical experience, technical expertise, and a commitment to quality and sustainability to fully harness its potential. Investing in the right type of iron wire, coupled with proper installation and maintenance, can lead to significant benefits, including increased durability, cost savings, and enhanced operational efficiency. As industries continue to evolve, iron wire's role will undoubtedly remain pivotal, driven by innovation and a steadfast focus on meeting the demands of modern society.