The versatility and reliability of 316 stainless steel wire have cemented its reputation as a cornerstone in various industrial and commercial applications. Its unique properties and superior performance standards make it a preferred choice, but what sets it apart, and how can stakeholders utilize its full potential? This article dives into the world of 316 stainless steel wire, unfolding its attributes through the lens of genuine user experience, industry expertise, and technical authority, fostering trust among professionals and enthusiasts alike.

Understanding the Composition
316 stainless steel wire is composed primarily of iron, supplemented by chromium, nickel, and molybdenum. The incorporation of molybdenum significantly enhances its corrosion resistance, especially in chloride-rich environments like coastal areas. This resilience makes it particularly suitable for marine applications, where exposure to saltwater is a constant threat. Its robust nature not only assures longevity but also maintains integrity under extreme conditions.
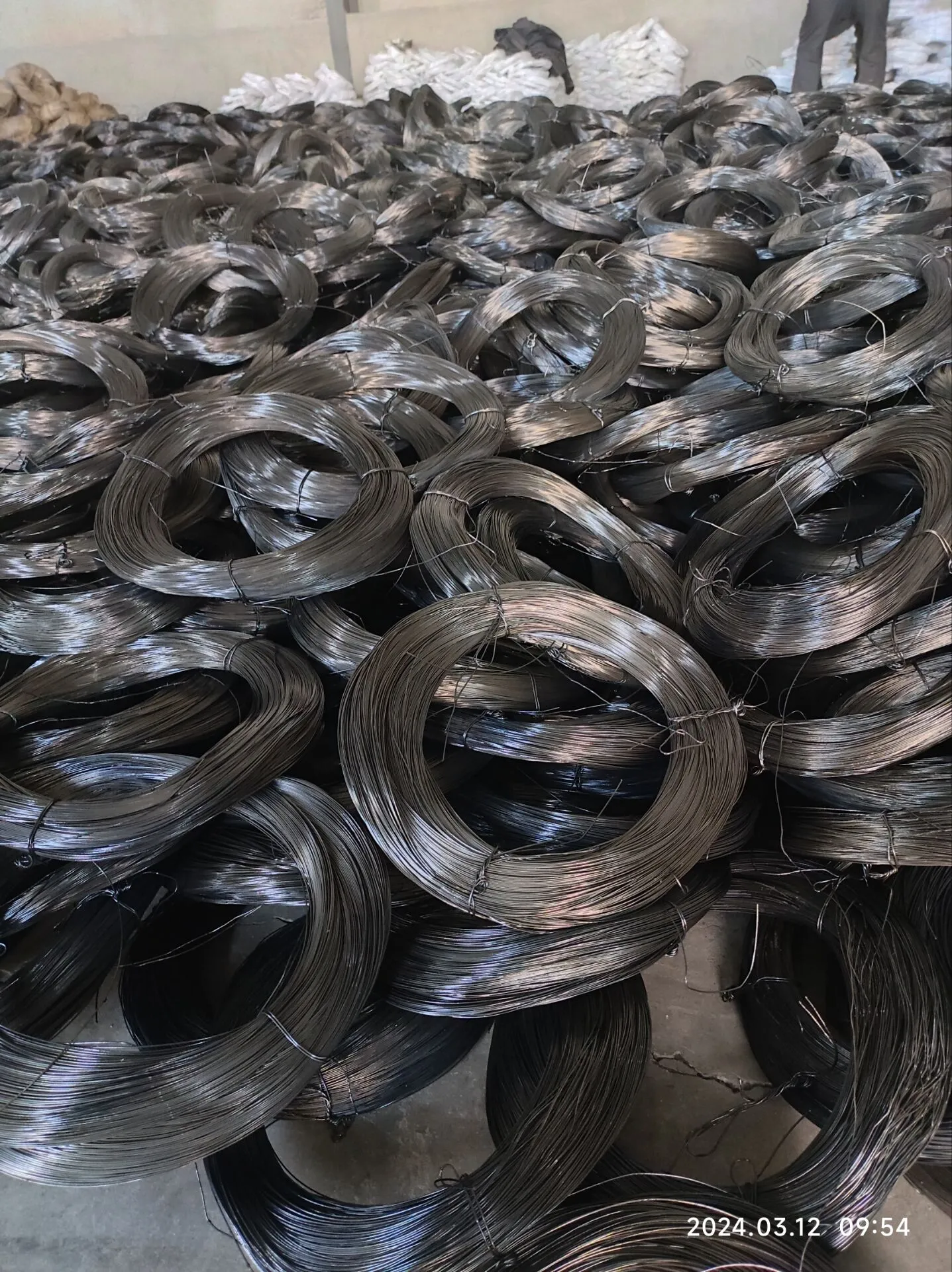
Real-World Applications and Experience
One of the most profound experiences with 316 stainless steel wire is in its application in the maritime industry. Shipbuilders and maritime engineers continuously rely on this grade due to its durability under relentless exposure to salty water. For instance, the maintenance team of a leading shipping company reported minimal corrosion-related repairs over a decade, attributing the reduced overhead costs to the material's superior performance. This practical application serves as a testament to its reliability and economic viability.
In the medical sector, its biocompatibility marks its significance. Instruments and surgical implants made from 316 stainless steel wire not only meet rigorous hygiene standards but also ensure patient safety. The diminished risk of infection and reaction, as corroborated by numerous medical practitioners, underscores its importance in healthcare. Surgeons from top medical institutions acknowledge the wire's precision and ease of shaping, aiding in complex procedures without compromising sterility or strength.
Expertise in Industrial Utilization
316 ss wire
Industrial experts highlight 316 stainless steel wire's robustness in manufacturing environments where chemical exposure is prevalent. Its resistance to acidic and alkaline substances makes it indispensable in chemical processing plants. A chemical engineer working with corrosive agents praised the material for its ability to withstand aggressive environments, thus curtailing frequent equipment wear and tear. This feedback loop from industrial users not only reinforces the material's standing but also identifies areas for potential innovations and improvements.
For high-temperature scenarios, its heat resistance is well-documented. Industrial ovens and heat exchangers are quintessential examples where 316 stainless steel wire performs exceptionally. A metallurgist specializing in thermal processing identified its stability at elevated temperatures as a critical factor, enabling consistent production outputs while minimizing service interruptions.
Authority of Standards and Compliance
When discussing the authoritativeness of 316 stainless steel wire, adhering to international standards such as ASTM and ISO is imperative. These guidelines assure users of the material's quality and performance benchmarks, facilitating global trade and confidence among buyers and manufacturers. Compliance with these standards is non-negotiable, reflecting in vendor selections and procurement policies by companies committed to quality assurance.
The trustworthiness of 316 stainless steel wire stems from its traceability and certification. Suppliers providing detailed documentation about their product's origin and manufacturing process enable end-users to make informed decisions. This transparency not only builds confidence in the product but also fosters long-term business relationships based on mutual trust and reliability.
In conclusion, 316 stainless steel wire stands out as a superior material choice due to its unique blend of properties, including corrosion and heat resistance, biocompatibility, and compliance with stringent standards. Real-world applications across diverse industries consistently validate its worth, with user experience and expert insights reinforcing its status as an indispensable component in modern engineering and manufacturing. As the material continues to evolve through technological advancements, its foundational attributes remain a guiding beacon for continuous innovation and trust.