Melting copper and aluminum together is a fascinating process that has sparked interest among DIY enthusiasts, metallurgists, and manufacturing industries alike. Both metals boast unique properties, with copper known for its superior electrical and thermal conductivity and aluminum being prized for its lightweight and corrosion-resistant characteristics. The idea of amalgamating these two promising elements intrigues those looking to exploit their combined strengths.
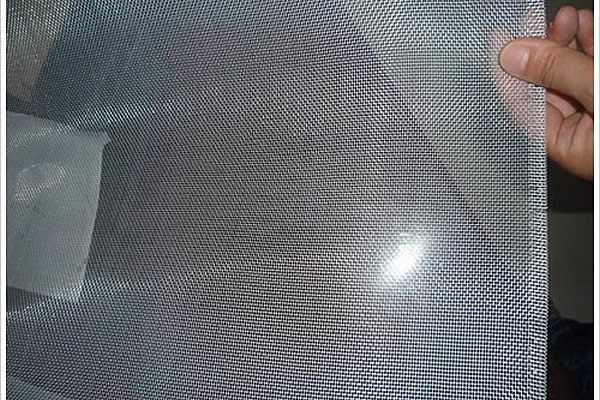
The process of melting copper and aluminum together is not as straightforward as it sounds due to their different melting points. Copper melts at approximately 1085 degrees Celsius, while aluminum melts at a lower temperature of around 660 degrees Celsius. To successfully combine these metals, one must carefully control the melting process to avoid complete liquefaction of aluminum before copper even begins to melt.
Industrial settings typically use induction furnaces or high-temperature kilns to perform this task. These devices offer precision temperature control, necessary for preventing unwanted alloying or oxidization, which can compromise the qualities of the resultant metal. For smaller-scale operations or experimental projects, a propane or oxy-acetylene torch can be used, though it comes with challenges in maintaining consistent temperatures and avoiding metal contamination.

When melted together in the right ratios,
copper and aluminum form a series of alloys collectively called aluminum bronzes. These distinct alloys combine the best properties of both parent metals and are widely utilized in applications demanding high strength, wear, and corrosion resistance. Industries such as marine hardware, electronic connectors, and aerospace components are prime examples of sectors that benefit from the unique properties of aluminum bronze.
From a DIY perspective, safety cannot be over-emphasized in the home setup for melting copper and aluminum. Appropriate personal protective equipment (PPE), including heavy-duty gloves, face shields, and heat-resistant clothing, is a must to protect against burns and inhalation of potentially harmful fumes. A well-ventilated area is essential to ensure the safe dissipation of smoke and fumes that may arise during the melting process.
melting copper and aluminum together
Another critical consideration is the degassing of the melt. Both copper and aluminum are prone to absorbing hydrogen, which can lead to undesirable porosity in the finished casting. Fluxing agents such as lithium-based fluxes are often employed during the melting to reduce oxides and allow gases to escape from the liquid metal, ensuring a dense and defect-free alloy.
The act of casting the molten blend, whether for artistic sculpting or industrial component fabrication, requires precision molds. These molds are typically constructed from refractory materials capable of withstanding high temperatures without degrading. Investment casting is a favored technique, offering excellent detail and surface finish for complex shapes. Alternatively, sand casting provides a more straightforward approach for larger, less intricate designs.
In advancing this metallurgical adventure, innovation often drives new alloying journeys, seeking optimal melting and blending methods to enhance the beneficial traits of copper and aluminum. Research into ecological effects also plays a pivotal role as industries strive to develop sustainable methods that minimize environmental impact.
Whether you're an aspiring metallurgist or someone captivated by the potential of combining metals, melting copper and aluminum is an exploration that extends beyond mere curiosity. With careful experimentation and attention to industrial practices, one might uncover previously untapped applications and innovations that leverage the full potential of these remarkable materials.