In the ever-evolving landscape of industrial welding, MIG cast iron wire holds a pivotal role in shaping the efficiency and quality of metal fabrication processes. As industries worldwide seek innovative solutions to bolster their production capabilities, the MIG cast iron wire emerges as a beacon of technological advancement and precision.
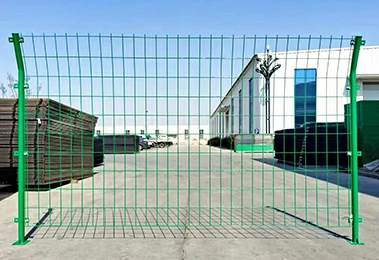
MIG, or Metal Inert Gas welding, is a technique revered for its versatility and effectiveness. It is particularly adept at working with a variety of metals, and cast iron is no exception. Cast iron, with its high carbon content and solidification properties, demands a precise and controlled approach to welding, which MIG cast iron wire provides with seamless competence.
The primary edge that MIG cast iron wire brings to the table is its exceptional ability to deliver strong and durable welds in cast iron materials. This wire is engineered to accommodate the inherent brittleness and different alloy composition of cast iron, ensuring that the welded joints exhibit both toughness and longevity. Such characteristics are indispensable in industries where cast iron is prevalent, such as automotive, construction, and heavy machinery.

One of the transformative experiences with MIG cast iron wire is its ease of use. Compared to traditional welding methods, it requires minimal cleanup and post-weld treatment, significantly reducing labor and production costs. Welders appreciate the consistent feed and stable arc that MIG cast iron wire offers, resulting in an impeccable bead formation and minimal spatter—an experience that enhances productivity and reduces downtimes due to welding defects.
mig cast iron wire
A hallmark of professional expertise in utilizing MIG cast iron wire lies in understanding the nuances of preheat and post-weld cooling. For cast iron, preventing the introduction of stress and cracks is imperative. Preheating the metal prior to welding and ensuring a controlled cooling environment are critical steps that skilled welders incorporate to leverage the full potential of the MIG cast iron wire. This practice not only elevates the quality of the welds but also prolongs the service life of the joined components.
In terms of authoritativeness, the MIG cast iron wire is backed by extensive research and development carried out by leading manufacturers in the welding industry. Companies invest in rigorous testing and technological innovations to enhance the wire's compatibility with various cast iron alloys, thus certifying its effectiveness and safety in diverse applications. The industry's endorsement of MIG cast iron wire as a reliable solution underscores its pivotal role in modern welding operations.
Trustworthiness in welding products is paramount, and MIG cast iron wire stands tall with a commendable track record of performance and safety. Users can trust that when employing this wire, they are equipped with a tool that meets stringent industry standards and regulatory requirements. Its widespread adoption across multiple sectors is a testament to the trust that professionals place in its capability to deliver exceptional welds time and again.
In conclusion, MIG cast iron wire represents a sophisticated blend of technology and metallurgical science tailored to meet the demanding requirements of cast iron welding. It symbolizes a commitment to excellence, enabling industries to achieve superior results in their welding projects. For engineers and craftsmen who demand precision and reliability, MIG cast iron wire is more than just a tool—it is an indispensable asset in the pursuit of industrial ingenuity and craftsmanship.