Welding wrought iron with a flux core welder presents unique challenges and opportunities. The distinct properties of wrought iron, combined with the versatility of flux core welding, can lead to successful joint creation with proper techniques and knowledge.
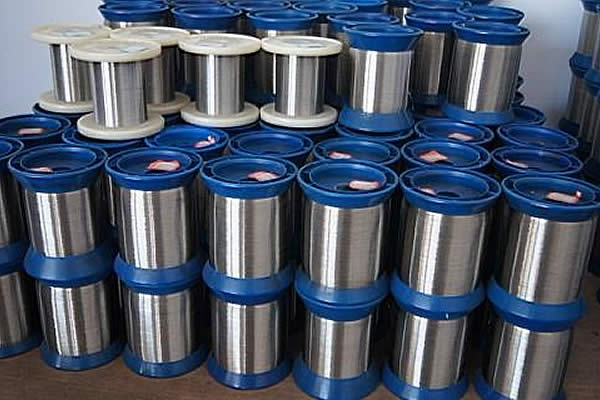
Understanding Wrought Iron
Wrought iron, often known for its use in ornamental and historic structures, is characterized by its fibrous inclusions and slag lines, giving it a unique grain. It is a material prized for its corrosion resistance and ductility, ideal for decorative gates, railings, and fencing. However, its low carbon content compared to steel alters its welding characteristics, requiring a precise approach to welding.

The Appeal of Flux Core Welding
Flux core arc welding (FCAW) is a favored method due to its versatility, especially in outdoor conditions where shielding gases may be less effective. The core contains fluxing agents, and other essential ingredients allow for a visually appealing and strong weld. In addition, it reduces the need for a shielding gas, making it more portable and practical for repairs and installations without additional equipment.
Prioritizing Safety and Preparation
Safety and thorough preparation are paramount before embarking on any welding project, especially with flux core welding of wrought iron. Safety equipment should include welding helmets with proper shade lenses, gloves, flame-resistant clothing, and respirators when in poorly ventilated areas. Furthermore, ensuring the welding area is clean and free of flammable materials is crucial.
Joint Preparation and Machine Settings
Achieving a quality weld on wrought iron begins with meticulous joint preparation. Cleaning the surfaces to remove any rust, paint, or grease is essential, preventing contamination of the weld pool. Proper joint design, typically involving V-grooves or lap joints, is critical to accommodate the unique nature of wrought iron. Ensuring a secure clamping system will maintain alignment throughout the welding process.
The welding machine should be configured for the task, with amperage settings fine-tuned based on the wrought iron's thickness and the filler wire used. Generally, starting with a lower amperage helps minimize slag inclusion and porosity, common issues with wrought iron.
welding wrought iron with flux core
Welding Technique Striking the Arc
Striking a stable arc is critical when welding wrought iron using flux core. The technique should involve a dragging motion, pulling the wire along the weld line at a consistent speed to ensure even distribution of the filler material and flux. Maintaining a steady angle, typically at around 15 degrees with respect to the workpiece, helps control the weld puddle and prevent running.
Heat Control and Interpass Temperatures
Control over heat input is vital when working with wrought iron to prevent potential warping or weakening. This involves not only setting the appropriate amperage but also monitoring the interpass temperatures. Implementing short welding segments allows for better heat management, reducing the risk of cracking due to the differential expansion of wrought iron and filler materials.
Post-Weld Care and Inspection
Post-weld treatment is essential for ensuring the longevity of wrought iron welds. Slag removal is necessary using a chipping hammer and brush to reveal the quality of the weld. Visual inspection should focus on identifying common issues such as undercut, porosity, or incomplete fusion, which can be rectified with additional passes if necessary.
Final treatments may include grinding for a more refined finish, and applying protective coatings to enhance corrosion resistance. For historical or artistic pieces, matching the final texture and color of surrounding areas is essential to maintain aesthetic continuity.
Building Expertise and Trust in Wrought Iron Welding
Developing proficiency in welding wrought iron with a flux core setup hinges on experience and continuous learning. Engaging with welding forums, professional courses, and manuals on welding techniques can enhance skills and problem-solving capabilities. Simultaneously, sharing insights and experiences within industry groups builds a reputation for trust and authority, establishing respect and credibility among peers.
Ultimately, by mastering the nuances of wrought iron and leveraging the advantages of flux core welding, welders can confidently tackle projects that demand both structural integrity and decorative finesse, ensuring their work stands the test of time.